What is Porosity in Welding: Crucial Tips for Achieving Flawless Welds
What is Porosity in Welding: Crucial Tips for Achieving Flawless Welds
Blog Article
Porosity in Welding: Identifying Common Issues and Implementing Ideal Practices for Avoidance
Porosity in welding is a pervasive problem that commonly goes undetected until it causes considerable issues with the honesty of welds. In this conversation, we will certainly check out the essential elements adding to porosity formation, examine its destructive impacts on weld efficiency, and talk about the ideal practices that can be embraced to lessen porosity incident in welding procedures.
Common Reasons of Porosity

One more constant offender behind porosity is the visibility of impurities on the surface area of the base metal, such as oil, grease, or corrosion. When these pollutants are not efficiently eliminated before welding, they can vaporize and come to be caught in the weld, creating problems. Utilizing filthy or damp filler materials can introduce impurities right into the weld, contributing to porosity concerns. To minimize these typical sources of porosity, detailed cleansing of base steels, proper protecting gas selection, and adherence to optimal welding parameters are crucial practices in achieving top notch, porosity-free welds.
Effect of Porosity on Weld Quality

The visibility of porosity in welding can substantially endanger the architectural stability and mechanical properties of bonded joints. Porosity develops voids within the weld metal, compromising its total stamina and load-bearing ability. These gaps serve as anxiety focus points, making the weld much more prone to fracturing and failure under used lots. Furthermore, porosity can decrease the weld's resistance to rust and other ecological factors, better diminishing its longevity and performance.
Welds with high porosity degrees often tend to show reduced effect stamina and minimized ability to warp plastically prior to fracturing. Porosity can hinder the weld's capability to properly transmit pressures, leading to early weld failure and prospective safety and security dangers in crucial frameworks.
Best Practices for Porosity Prevention
To boost the architectural integrity and top quality of welded joints, what certain actions can be applied to decrease the event of porosity throughout the welding process? Utilizing the proper welding strategy for the specific material being bonded, such as adjusting the welding angle and gun placement, can even more avoid porosity. Regular inspection of welds and immediate removal of any issues determined during the welding process are vital methods to avoid porosity and generate premium welds.
Importance of Correct Welding Methods
Executing proper welding her latest blog strategies is vital in making sure the architectural honesty and top quality of bonded joints, building on the foundation of efficient porosity avoidance measures. Welding techniques straight affect the overall toughness and sturdiness of the bonded framework. One crucial element of proper welding strategies is keeping the appropriate warm input. Too much heat can cause enhanced porosity as a result of the entrapment of gases in the weld pool. Alternatively, inadequate warmth might lead to incomplete fusion, developing prospective powerlessness in the joint. In addition, making use of the ideal welding parameters, Get the facts such as voltage, current, and travel speed, is essential for achieving audio welds with very little porosity.
In addition, the choice of welding procedure, whether it be MIG, TIG, or stick welding, should line up with the details requirements of the job to ensure ideal outcomes. Proper cleaning and prep work of the base metal, along with choosing the best filler product, are also vital parts of skilled welding techniques. By adhering to these finest techniques, welders can minimize the risk of porosity formation and generate high-quality, structurally sound welds.
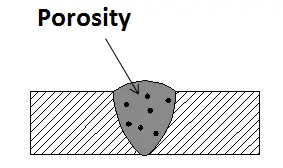
Checking and Top Quality Control Actions
Quality article control steps play a crucial function in confirming the honesty and integrity of bonded joints. Testing procedures are important to discover and stop porosity in welding, making sure the toughness and toughness of the final product. Non-destructive testing techniques such as ultrasonic testing, radiographic testing, and aesthetic evaluation are commonly used to recognize possible issues like porosity. These strategies permit for the evaluation of weld high quality without compromising the stability of the joint. What is Porosity.
Conducting pre-weld and post-weld assessments is likewise essential in maintaining quality assurance standards. Pre-weld evaluations include confirming the materials, tools settings, and sanitation of the workplace to stop contamination. Post-weld inspections, on the various other hand, evaluate the last weld for any type of issues, including porosity, and validate that it satisfies specified standards. Implementing a thorough quality assurance strategy that includes detailed testing treatments and inspections is vital to reducing porosity problems and making certain the total high quality of welded joints.
Final Thought
Finally, porosity in welding can be an usual concern that impacts the top quality of welds. By recognizing the usual reasons for porosity and implementing best practices for prevention, such as proper welding techniques and testing steps, welders can guarantee excellent quality and reputable welds. It is necessary to focus on avoidance methods to lessen the occurrence of porosity and preserve the stability of welded structures.
Report this page